Keeping it cool: revitalizing the traditional Okinawan craft of bashofu
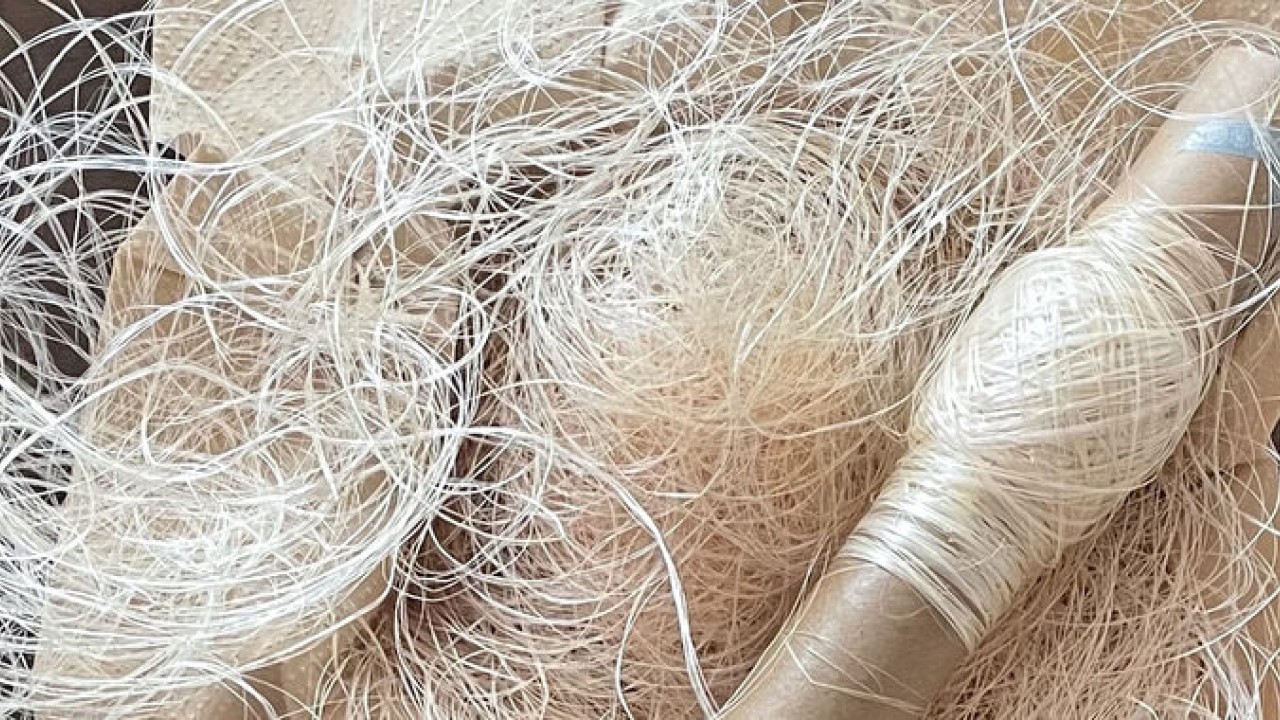
The islands of Okinawa, the Southernmost prefecture of Japan, are well known for their hot, humid summers. These days, locals and tourists retreat from the oppressive heat into buildings cooled by air conditioning, but during the time of the Ryukyu Kingdom, people of all classes relied on a textile fabric called bashofu, to keep cool.
The bashofu fabric, which is traditionally used for kimonos, is made from Itobasho, a banana plant which is locally grown in Okinawa. The craft of making the fabric, Kijoka bashofu, was classified as an Important Intangible Cultural Property in 1974 and involves transforming the Itobasho plant fibers into threads of basho yarn, which are then woven into the textile fabric, bashofu. The resulting material has unique natural properties that are perfectly suited to the Okinawan climate.
“The material is highly breathable, as the part of the plant used to make the yarn contains many fiber cells. These fiber cells are long, hollow tubes, creating holes that sweat can evaporate through, which cools and dries the fabric,” said Dr. Yoko Nomura, a researcher in the OIST Science and Technology Group, who studies the structural and chemical properties of the material, with support from Dr. Koji Koizumi of the OIST Scientific Imaging Section.
However, in recent years, production of bashofu fabric has slowed. Many practitioners of the craft are aging elders, who are growing unable to carry out the slow and difficult process.
“It takes over 23 steps to get from cultivating the plant to finishing the final clothing, and every step is carefully and painstakingly done by hand,” explained Ms. Hitomi Shinzato, a research unit administrator at OIST. “The method used today hasn’t changed much since it was first developed in the 13th or 14th century.”
Fewer people are working in the fields to cultivate the Itobasho plant, Ms. Shinzato added, so the yield of raw material has also dropped.
In order to address this shortage Dr. Nomura and Ms. Shinzato are researching new methods to increase the production of basho yarn, with the help of machines.
The team is developing biotechnology to extract fibers from Itobasho in a way that is efficient and environmentally friendly. They are also establishing new ways to spin the extracted fibers into basho yarn, using machinery.
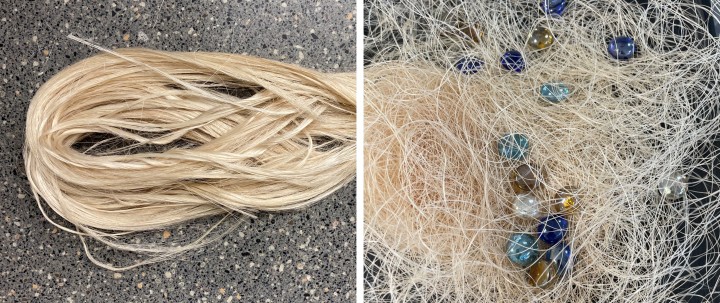
Traditionally, the yarn is then hand-woven into the fabric, but the OIST team are now exploring whether the material is tough enough to be made into textiles by using industrial weaving machines.
“This is the first time that basho yarn will be woven using conventional machines, so we don’t know how it will turn out,” said Ms. Shinzato.
For the first shirt, a mixture of basho and other yarns – a similar yarn to basho – will be used, but a shirt made fully from basho yarn is the ultimate goal.
The yarn will soon be woven by AKAI Inc. in Kyoto to make a traditional Okinawan Kariyushi shirt, in collaboration with Mr. Kakazu, a representative of LEQUIO Ltd., a local Okinawan resort-wear clothing brand. By showing that the basho threads can be used to make everyday clothing, like Kariyushi, the researchers hope that a new generation of Okinawans will be exposed to the material, and its unique cooling properties.
“Young people, even in Okinawa, don’t know very much about bashofu,” said Dr. Nomura. “So this is a good chance for them to learn about traditional bashofu from seeing this new, machine-made basho textile.”
The team also plan to provide the yarn to weavers in Okinawa and beyond, for use in producing their own products.
Currently, the project is supported financially by Furusato Shinko Kikin, the Bank of Okinawa, but the team is also raising funds to manufacture the shirts through the sale of a booklet, “MUSA weavers’ hands: Science and Wisdom of Our Forefathers”.
The booklet explores the cultural and historical significance of kijoka bashofu, including detailed descriptions of each step in producing the textile. It also discusses some of the cutting-edge scientific techniques used to probe the properties of the textile.
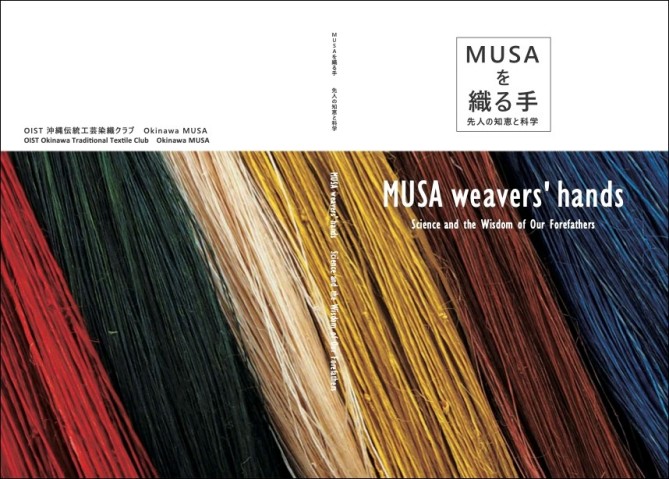
If you would like to learn more or support the project by purchasing the booklet, please visit the OIST website pages for Okinawa Musa - Itobasho Projects.
For press enquiries:
Press Inquiry Form